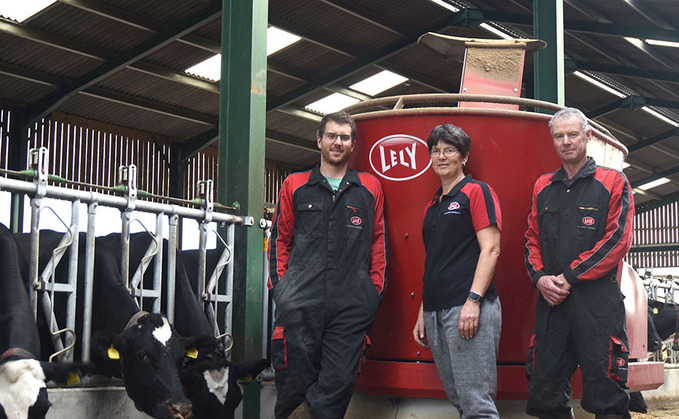
An automated feeding system is proving its worth on a Shropshire farm where yields, cow health and feeding efficiencies have been given a boost. Replacing a mixer wagon with an automatic feeding system...
An automated feeding system is proving its worth on a Shropshire farm where yields, cow health and feeding efficiencies have been given a boost. Replacing a mixer wagon with an automatic feeding system...
Outdoor Beef Finishing Coral System, available